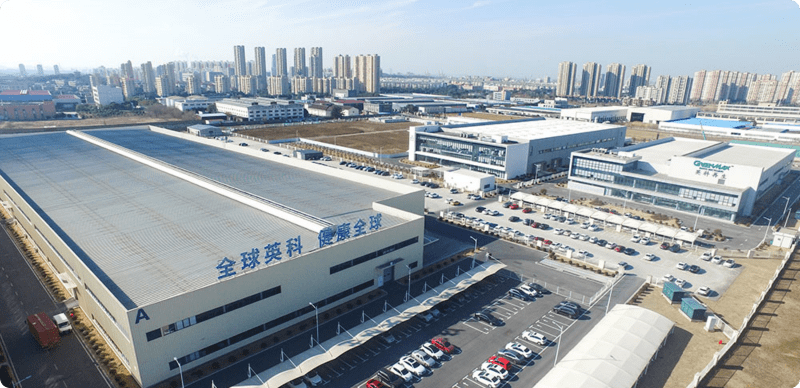
Flexible Manufacturing
Flexible manufacturing ensures that in the face of changing market demand and production capacity constraints,production plans can be flexibly adjusted to quickly respond to market changes, shorten the cycle of the product from design to market, and maintain efficient production operations.
-
Production Scheduling Capabilities
We can flexibly adjust production lines, equipments and human resources.
This means that we can quickly increase or decrease the number of production lines, adjust worker shifts, and redistribute materials.
We can switch to produce different products without the need for large-scale modifications on the production line, adapt to diverse product designs.
-
Product Design
Experienced packaging designers can help customers complete product design.
We provide design and manufacturing integration services. Customers can choose to provide their packaging,or we can help design, to simplify the customer’s investment in the product.
-
Process Capacity
We choose high polymers as the main raw materials for cold and hot compress products, which are soft and elastic enough for both cold and hot use.
Packaging technology is the key to cold and hot compress gel products, which ensures that the gel will not leak and the package remains intact during use.
We choose durable and soft packaging materials to suit the skin fit. Usually, high-frequency melting or heat sealing technology is used to seal the plastic bag or cloth bag.
Product supporting protective equipment can not only package the product when used, but also be used to preserve the product on a daily basis.
Multiple quality control procedures ensure that each product can meet the corresponding safety and efficiency standards, and it still does not freeze under the condition of -18°C.
-
Supply Chain Scheduling Capacity
Effective supply chain scheduling enables us to make better use of our production resources.
By coordinating different suppliers, production units and distributors, we can ensure that the implementation of the production plan is coordinated with other links in the supply chain.
Thus, the circulation of raw materials, parts and final products in the production process can be timely and efficient.